Altijd vooroplopen op het gebied van hightech-ontwikkelingen en innovatief bezig zijn. En regelmatig de eerste op de wereld zijn die een bepaalde techniek of proces toepast. Dat is zo’n beetje het credo van de Engineering & Maintenance Division (E&M) van KLM. Daar op excursie gaan is geen straf als je geïnteresseerd bent in het nieuwste van het nieuwste op het gebied van onderhoud aan vliegtuigmotoren.
Gastheer van deze excursie is Marcel van Wonderen, Master Engineer bij de afdeling Process, Equipment & Materials Development. Hij omschrijft zijn afdeling als een soort onafhankelijk ingenieursbureau, dat zoveel mogelijk objectief kijkt naar technologische ontwikkelingen en kansen om werkprocessen en technieken toe te passen die de hoogste kwaliteit en betrouwbaarheid opleveren. Gelet op de extreme condities waaraan vliegtuigmotoren worden blootgesteld, is het geen overbodige luxe om extreme eisen te stellen aan de toegepaste oppervlaktetechnieken op de motoronderdelen.
Was het vroeger chroom wat de klok sloeg bij de behandeling van de motoronderdelen, tegenwoordig wordt daarbij helemaal geen chroom meer toegepast. Voor vliegtuigmotoronderdelen bleek het mogelijk geschikte alternatieven te vinden. Gedurende de afgelopen tien jaar is chroom helemaal vervangen door thermisch spuiten, waarvan HVOF (High Velocity Oxygen Fuel) en plasmaspuiten de belangrijkste processen zijn. “Zo’n 60 tot 70 procent van alle onderdelen van een vliegtuigmotor krijgt een coating door thermisch spuiten”, zegt Marcel van Wonderen. “Dat is ongekend. Een vliegtuigmotor kan niet meer vliegen zonder thermisch spuitcoatings; die coatings vormen een integraal onderdeel van het ontwerp van de motor. Bij nog enkele toepassingen wordt nickel plating ingezet. En we zijn bezig om meer toepassingen te vinden voor lasercladding. Sinds kort passen we ook Wire EB-welding toe om een laag aan te brengen. Dat is een heel mooie techniek en daarmee zijn we als KLM E&M weer één van de eerste op de wereld die dit toepassen op vliegtuigmotordelen.”

ALTERNATIEVEN VOOR CHROOM
Hij wijst erop dat het langzaamaan in de ban doen van chroom te danken is aan het Europarlement en REACH, maar nog veel meer aan internationale luchtvaartconferenties met als voortrekkers de vliegtuigonderhoudswereld uit de VS en Canada. “Ik ben lid geweest van het Amerikaanse HCAT (Hard Chrome Alternative Team) dat systematisch onderzoek naar alternatieven in gang zette. Na veel onderzoek en testen kwam daaruit dat bijvoorbeeld het HVOF-proces een heel goed alternatief is voor alle chroomlagen. Verchromen is ook een ontzettend oud proces, dat op basis van allerlei technische studies heel lang te boek heeft gestaan als dé oplossing voor veel verschillende problemen die te maken hadden met slijtage, door welke oorzaak dan ook. Men dacht altijd in chroom, maar chroom blijkt, ook achteraf, technisch gezien niet altijd de optimale oplossing te zijn. Het was een alleskunner, een gemiddelde alleskunner die nergens uitblonk, maar wel nadelig was voor mens en milieu. Uit allerlei rapporten van de OSHA (Occupational Safety and Health Administration) die in de VS zijn geschreven, blijkt dat er in de loop van 30 jaar ongeveer 3.000 galvaniseurs in de VS zijn overleden door kanker gerelateerd aan hexavalent chroom.”
Nadat was bewezen dat HVOF-coatings een heel goed alternatief zijn voor chroom, is Van Wonderen in samenwerking met General Electric (één van de grote vliegtuigmotoren OEM’s), gaan zoeken naar in de praktijk bruikbare oplossingen, die voor allerlei soorten slijtageproblemen nog beter scoorden dan chroom. Gevolg hiervan was dat voor iedere soort slijtage (abrasie, erosie, vreten, glijdende inslag, enzovoorts) een specifieke coating werd ontwikkeld die met thermisch spuiten wordt aangebracht. Dus geen gemiddelde alleskunner meer, maar to the pointmaterialen voor specifieke toepassingen, zoals Triballoy 800, wolfraamcarbide/kobalt, wolfraamcarbide/kobaltchroom en Inconel718. Al die materialen zijn specifiek voor een bepaalde functionaliteit.

FUNCTIONALITEIT
Volgens Van Wonderen is functionaliteit het toverwoord. “Die functionaliteit kun je definiëren als je het juiste slijtagemechanisme kent en ook nog eens in samenhang met temperatuur en corrosie. Die drie en de combinatie daarvan bepalen alles. Er zijn zo’n 15 verschillende vormen van slijtage die je dus in samenhang moet beschouwen met temperatuur en allerlei vormen van corrosie. Het mooie aan thermisch spuiten is dat we elke gewenste functionaliteit kunnen spuiten. Als chroomvervanger is HVOF de meest gekozen oplossing.” Enkele voorbeelden: voor een tribologische functionaliteit, waarbij dus rekening wordt gehouden met zowel slijtage als wrijving en smeringseffecten, wordt nu Tribaloy 400 ingezet bij lage temperatuurtoepassingen. Bij eenzelfde functionaliteit, maar met hoge temperatuurtoepassing, zoals bij turbinedelen, wordt Tribaloy 800 ingezet, en voor ‘sliding wear’ kies je voor wolfraamcarbide/kobalt. Als een keramische coating gewenst is, bijvoorbeeld voor onderdelen in de verbrandingskamer van de motor, zul je dat niet met HVOF doen, maar moet je altijd het plasmaspuiten toepassen. Op het gebied van thermisch spuiten heeft KLM vijf technieken in huis: plasmaspuiten, draadvlamspuiten, poedervlamspuiten, elektrisch boogspuiten en HVOF-spuiten. Afhankelijk van de functionaliteit wordt één van de processen gekozen.
VOOROPLOPEN
“We hebben de alternatieven voor elkaar kunnen krijgen, omdat we als afdeling altijd met innovatieve ontwikkelingen bezig zijn. Tachtig procent van ons werk is gericht op productie-ondersteuning en twintig procent van onze tijd is gericht op innovatie. Bij mijn afdeling willen wij altijd vooroplopen om te kijken welke hightechoplossingen wij kunnen toepassen. Je kunt zeggen dat onze afdeling ‘Engineering Team Production Support’ binnen KLM E&M in de wereld van onderhoud van vliegtuigmotoren vooroploopt en dat wij continu proberen om de allernieuwste technieken in huis te krijgen. Dat blijft internationaal ook niet onopgemerkt, want ik word vaak gevraagd om lezingen te geven over de technieken die wij toepassen. Daarnaast: 60 tot 70 procent van ons onderhoudswerk is voor derden, dus voor andere luchtvaartmaatschappijen dan KLM.”
De vraag is natuurlijk wel hoe de voorbehandeling eruitziet bij de thermisch spuitcoatings. Dat is van belang, omdat het aanbrengen van dergelijke coatings stress oplevert in de vorm van trekspanningen, wat de vermoeiingssterkte van een onderdeel nadelig beïnvloedt. Om dat te compenseren, wordt er eerst shotpeening toegepast: er worden kleine kogeltjes met hoge snelheid tegen het metaal geschoten, waardoor het substraat vervormt en daardoor zichzelf verstevigt. Het shotpeenen vooraf is dus heel belangrijk. Daarna is er een activatieproces met grit, om de natuurlijke oxidehuid van het metaaloppervlak te verwijderen, waardoor de hechting van de thermisch gespoten coating enorm verbetert. Na het thermisch spuiten wordt in negen van de tien gevallen de coating nog nageslepen met diamanten slijpschijven, om tot de juiste dimensie te komen ten behoeve van de voorgeschreven geometrische afmetingen. Bij keramische coatings is naslijpen niet nodig.

LAAGDIKTE EN HARDHEID
Een ander voordeel van thermisch spuiten, is dat je kunt kiezen uit veel verschillende laagdikten. Bij chroom kon je in de regel niet verder gaan dan 300 micrometer, maar bij thermisch spuiten kun je qua laagdikte kiezen uit een reikwijdte van 0,05 millimeter tot wel 10 millimeter. Elk proces heeft z’n optimale laagdikte: bij HVOF kom je niet hoger dan 0,3 - 0,35 millimeter, bij elektrisch draadspuiten kun je makkelijk tot 1,5 millimeter spuiten en bijvoorbeeld een polyesteraluminium coating als slijtwillige laag wordt wel gespoten tot 6 millimeter dikte. Verder kan er op bijna elk soort materiaal gespoten worden. Metalen, niet-metalen, carbides, keramieken en kunststoffen kunnen met thermisch spuiten behandeld worden. Weliswaar kunnen thermisch gespoten coatings de hechtsterkte van chroom niet halen (het gaat meer om de functionaliteit bij verschillende toepassingen), maar volgens Van Wonderen kun je met HVOF toch nog een treksterkte halen tot 70 MPa met een dichtheid van 0,3 procent porositeit. Bij plasmaspuiten kun je afhankelijk van de materiaalsoort tot zo’n 50 – 60 MPa komen.
“Bij thermisch spuiten heb je alleen een mechanische hechting (bij chroom een metallurgische hechting), maar is vooral micro- en macrohardheid een belangrijke eigenschap. Bij HVOF, en dan in het bijzonder wolfraamcarbide/kobalt, is die hardheid erg hoog. Die eigenschap heb je ook nodig, want als je erosie of abrasie als functionaliteit hebt, dan moeten oppervlakken van motordelen beschermd worden tegen zanddeeltjes die in de motor komen. Het oppervlak moet dan keihard en dus slijtvast zijn. Wolfraamcarbide/kobalt is dat ook, het is bijna zo hard als diamant. Vandaar dat het alleen naslijpbaar is met diamant.”

DRUK VAN 3.800 BAR
Al wandelend door de hal zijn we terechtgekomen bij een unieke machine met een geavanceerd proces, waarvoor KLM als eerste in de wereld goedkeuring kreeg van General Electric om het toe te passen op hun motoronderdelen. Het gaat om een machine waarin het UHPW-proces (ultra high pressure waterjetting) wordt uitgevoerd, om onderdelen met een thermisch spuitcoating weer helemaal schoon te krijgen wanneer die coating weer vernieuwd moet worden. Vroeger moesten die lagen verwijderd worden met gritstralen of via chemische baden, waar ze soms drie dagen in moesten liggen. Nu kan KLM die onderdelen in de machine in een half uur schoon krijgen, dankzij een waterjetstraal met een druk van 3.800 bar, een watersnelheid van 800 meter per seconde (bijna drie keer de geluidssnelheid) en een roterende nozzle die op 1.500 toeren draait. Dat laatste levert een vlakke energiedistributie op. Het resultaat hiervan is dat de meeste thermisch spuitcoatings op deze manier eraf geblazen kunnen worden, zonder het moedermateriaal te beschadigen.
Marcel van Wonderen: “We zijn zeker tevreden met deze machine, maar nu is de allernieuwste technologie beschikbaar op dat gebied en we kijken of we de machine daarvoor gaan aanschaffen. Het gaat dan om HFFPW (high frequency forced pulse waterjetting), waarmee een nog grotere kracht wordt uitgeoefend met het water, waardoor we de coating nog sneller kunnen verwijderen. De HVOF-coatings zijn verschrikkelijk sterk en hard en we kunnen ze met de huidige UHPW-machine niet verwijderen, maar met de pulse waterjetting technologie wel.”
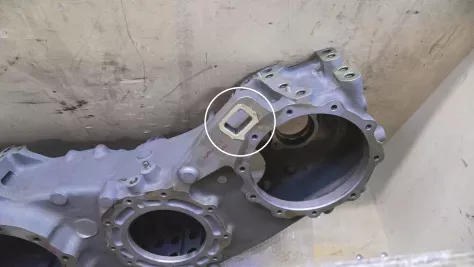
COLD SPRAY
Een andere nieuwe technologie op het gebied van coatings waar Van Wonderen naar kijkt, is het cold spray proces (zie ook het artikel 'Toepassing copper cold spray in zonnepanelen' in de bijlage), meer specifiek het Gas Dynamic Cold Spray proces. “Ik ben ervan overtuigd dat die technologie een groot potentieel aan mogelijkheden heeft voor ons werk. Het is een proces met de voordelen van thermisch spuiten en lasercladden, zonder de nadelen ervan. Vanochtend hadden we een Brits technologisch instituut (TWI) – vergelijkbaar met TNO in Nederland – op bezoek om met ons te kijken of we die technologie samen verder zouden kunnen ontwikkelen voor toepassing bij motordeelreparaties. Momenteel hebben we al testen lopen bij Dycomet in Friesland, een bedrijf dat apparatuur levert om cold spray toe te passen.”
Cold spray biedt voordelen die met thermisch spuiten niet bereikbaar zijn. Je kunt het ook gebruiken als alternatief voor galvanische processen. Daarnaast kun je met cold spray aan structural repair doen, dat willen zeggen dat je er de sterkte van het moedermateriaal mee kunt herstellen, iets wat met thermisch spuiten onmogelijk is. Tot slot is cold spray ook inzetbaar voor additive manufacturing. Nu wordt er in de industrie vooral gebruikgemaakt van laserpoederbedprinting, maar dat proces gaat veel langzamer dan cold spraying. Van Wonderen spreekt de verwachting uit dat de apparatuur voor cold spray nog dit jaar door KLM E&M zal worden aangeschaft.